What is a press break?
A press break is a machine that bends sheet metal into various shapes. It is used in a variety of industries, including automotive, aerospace, and construction.
Press breaks work by applying pressure to the sheet metal, causing it to bend. The amount of pressure and the shape of the bend are controlled by the operator of the machine.
Press breaks are an important tool for many industries. They allow manufacturers to create complex shapes from sheet metal, which would be difficult or impossible to do by hand.
Here are some of the benefits of using a press break:
- Increased accuracy
- Reduced labor costs
- Improved quality
- Faster production times
Press breaks have been around for centuries. The first press brakes were developed in the 18th century. These early machines were hand-powered and used to bend metal for a variety of purposes, including armor and tools.
Today, press brakes are powered by electricity or hydraulics. They are used to bend a wide variety of materials, including steel, aluminum, and stainless steel.
Press breaks are an essential tool for many industries. They allow manufacturers to create complex shapes from sheet metal, which would be difficult or impossible to do by hand.
Press Brake
A press brake is a machine that bends sheet metal into various shapes. It is used in a variety of industries, including automotive, aerospace, and construction.
- Bending
- Sheet metal
- Hydraulic
- Accuracy
- Efficiency
- Versatility
These key aspects highlight the importance of press brakes in the manufacturing industry. They are used to bend sheet metal into a variety of shapes, with high accuracy and efficiency. Press brakes are also versatile machines, capable of bending a wide range of materials and thicknesses.
For example, in the automotive industry, press brakes are used to create complex shapes for car bodies and other components. In the aerospace industry, press brakes are used to create parts for aircraft, such as wings and fuselages. And in the construction industry, press brakes are used to create parts for buildings, such as roofing and siding.
Press brakes are an essential tool for many industries. They allow manufacturers to create complex shapes from sheet metal, which would be difficult or impossible to do by hand.
1. Bending
Bending is the process of shaping a material by applying force to it, causing it to deform. It is a common manufacturing process used to create a variety of products, from simple brackets to complex automotive parts.
Press brakes are one of the most common types of bending machines. They use a punch and die to bend sheet metal into a variety of shapes. The punch is the part of the machine that applies force to the sheet metal, while the die is the part of the machine that supports the sheet metal and determines the shape of the bend.
Bending is an important part of the press brake process. It allows manufacturers to create complex shapes from sheet metal, which would be difficult or impossible to do by hand. Bending is also used to create features on sheet metal, such as holes and slots.
There are a number of different factors that affect the bending process, including the type of material being bent, the thickness of the material, and the shape of the bend. It is important to understand these factors in order to achieve the desired results.
Bending is a versatile process that can be used to create a wide variety of products. It is an important part of the press brake process, and it is essential for manufacturers to understand the factors that affect bending in order to achieve the desired results.
2. Sheet metal
Sheet metal is a thin metal sheet that is used in a variety of applications, including automotive, aerospace, and construction. It is typically made of steel, aluminum, or stainless steel.
Press brakes are machines that bend sheet metal into various shapes. They are used in a variety of industries, including automotive, aerospace, and construction.
The connection between sheet metal and press brakes is essential. Press brakes would not be able to function without sheet metal, and sheet metal would not be able to be shaped into complex forms without press brakes.
Here are some of the ways that sheet metal and press brakes are used together:
- In the automotive industry, press brakes are used to create complex shapes for car bodies and other components.
- In the aerospace industry, press brakes are used to create parts for aircraft, such as wings and fuselages.
- In the construction industry, press brakes are used to create parts for buildings, such as roofing and siding.
Sheet metal and press brakes are essential tools for many industries. They allow manufacturers to create complex shapes from sheet metal, which would be difficult or impossible to do by hand.
3. Hydraulic
Hydraulics is the use of fluid power to transmit energy. In a press brake, hydraulics is used to power the ram, which is the part of the machine that applies force to the sheet metal.
- Power
Hydraulic systems are very powerful. This makes them ideal for use in press brakes, which require a lot of force to bend sheet metal.
- Precision
Hydraulic systems are very precise. This allows press brakes to bend sheet metal to very tight tolerances.
- Controllability
Hydraulic systems are very controllable. This allows the operator of a press brake to precisely control the force and speed of the ram.
- Efficiency
Hydraulic systems are very efficient. This means that they can operate for long periods of time without overheating.
Hydraulics is an essential part of press brakes. It provides the power, precision, controllability, and efficiency that are necessary to bend sheet metal into complex shapes.
4. Accuracy
Accuracy is one of the most important aspects of press brake operation. It refers to the ability of a press brake to bend sheet metal to the desired dimensions and shape. Accuracy is essential for a number of reasons:
- Quality: Accurate bends ensure that the finished product meets the required quality standards.
- Efficiency: Accurate bends reduce the need for rework and scrap, which can save time and money.
- Safety: Accurate bends help to ensure that the finished product is safe to use.
There are a number of factors that affect the accuracy of a press brake, including:
- The condition of the machine: A well-maintained press brake will be more accurate than a machine that is not properly maintained.
- The tooling: The tooling used in a press brake can also affect accuracy. It is important to use the correct tooling for the job and to ensure that the tooling is in good condition.
- The operator: The skill of the operator can also affect accuracy. An experienced operator will be able to produce more accurate bends than a less experienced operator.
There are a number of things that can be done to improve the accuracy of a press brake, including:
- Regular maintenance: Regular maintenance can help to keep a press brake in good condition and ensure that it is operating accurately.
- Proper tooling: Using the correct tooling for the job and ensuring that the tooling is in good condition can help to improve accuracy.
- Operator training: Providing operators with training can help them to improve their skills and produce more accurate bends.
Accuracy is an essential aspect of press brake operation. By understanding the factors that affect accuracy and taking steps to improve accuracy, manufacturers can improve the quality of their products, save time and money, and ensure that their products are safe to use.
5. Efficiency
Efficiency is a measure of how well a machine or process converts energy into useful work. In the context of press brakes, efficiency is important because it affects the productivity and profitability of the manufacturing process.
- Reduced Cycle Time
One way that press brakes can improve efficiency is by reducing cycle time. Cycle time is the amount of time it takes to complete one bend. By reducing cycle time, manufacturers can increase the number of bends that can be produced per hour.
- Reduced Scrap
Another way that press brakes can improve efficiency is by reducing scrap. Scrap is material that is wasted during the manufacturing process. By reducing scrap, manufacturers can save money on materials and reduce the amount of waste that is produced.
- Improved Quality
Press brakes can also improve efficiency by improving quality. By producing high-quality bends, manufacturers can reduce the number of rejects and rework that is required. This can save time and money, and it can also improve the reputation of the manufacturer.
- Increased Productivity
Overall, press brakes can improve efficiency by increasing productivity. By reducing cycle time, reducing scrap, and improving quality, press brakes can help manufacturers to produce more products in a shorter amount of time and with less waste.
Efficiency is an important consideration for any manufacturer that uses press brakes. By understanding the factors that affect efficiency, manufacturers can take steps to improve the efficiency of their press brake operations and increase their productivity and profitability.
6. Versatility
Versatility is a key characteristic of press brakes. It refers to the ability of a press brake to bend a wide variety of materials and thicknesses. This versatility makes press brakes an essential tool for many industries, including automotive, aerospace, and construction.
There are a number of factors that contribute to the versatility of press brakes. One factor is the wide range of tooling that is available for press brakes. This tooling allows press brakes to bend a variety of materials, including steel, aluminum, and stainless steel. It also allows press brakes to bend a variety of thicknesses, from thin sheet metal to thick plate.
Another factor that contributes to the versatility of press brakes is their ability to be programmed to perform a variety of bends. This programmability allows press brakes to be used to create complex shapes and forms. It also allows press brakes to be used to bend parts that are difficult or impossible to bend by hand.
The versatility of press brakes makes them an essential tool for many industries. They are used to create a wide variety of products, from simple brackets to complex automotive parts. Press brakes are also used to create parts for a variety of industries, including aerospace, construction, and medical.The versatility of press brakes is a key factor in their popularity. It allows manufacturers to use press brakes to create a wide variety of products, from simple to complex. Press brakes are also a versatile tool that can be used in a variety of industries.
Frequently Asked Questions about Press Brakes
Press brakes are essential machines in many industries, but they can also be complex and expensive. Here are answers to some of the most common questions about press brakes:
Question 1: What is a press brake?
A press brake is a machine that bends sheet metal into various shapes. It is used in a variety of industries, including automotive, aerospace, and construction.
Question 2: How does a press brake work?
A press brake works by applying pressure to the sheet metal, causing it to bend. The amount of pressure and the shape of the bend are controlled by the operator of the machine.
Question 3: What are the different types of press brakes?
There are two main types of press brakes: mechanical press brakes and hydraulic press brakes. Mechanical press brakes use a flywheel to generate the force needed to bend the sheet metal. Hydraulic press brakes use a hydraulic cylinder to generate the force.
Question 4: What are the advantages of using a press brake?
There are many advantages to using a press brake, including increased accuracy, reduced labor costs, improved quality, and faster production times.
Question 5: What are the safety considerations when using a press brake?
There are a number of safety considerations when using a press brake, including wearing proper safety gear, keeping hands and fingers away from the moving parts of the machine, and being aware of the potential for pinch points.
These are just a few of the most common questions about press brakes. If you have any other questions, please consult with a qualified professional.
Summary: Press brakes are essential machines in many industries, but they can also be complex and expensive. It is important to understand the different types of press brakes, the advantages and disadvantages of each type, and the safety considerations when using a press brake.
Transition to the next article section: Now that you have a basic understanding of press brakes, you can learn more about their specific applications in various industries.
Conclusion
As we have explored in this article, press brakes are essential machines in a wide range of industries, from automotive to aerospace to construction. They offer a number of advantages over other bending methods, including increased accuracy, reduced labor costs, improved quality, and faster production times.
Press brakes are complex machines, but they are also versatile and relatively easy to use. With proper training, operators can quickly learn how to operate a press brake safely and efficiently. If you are considering investing in a press brake, be sure to do your research and choose a machine that is right for your needs.
The future of press brakes is bright. As technology continues to advance, we can expect to see even more innovative and efficient press brakes on the market. These machines will play an increasingly important role in the manufacturing industry, helping to create the products we use every day.
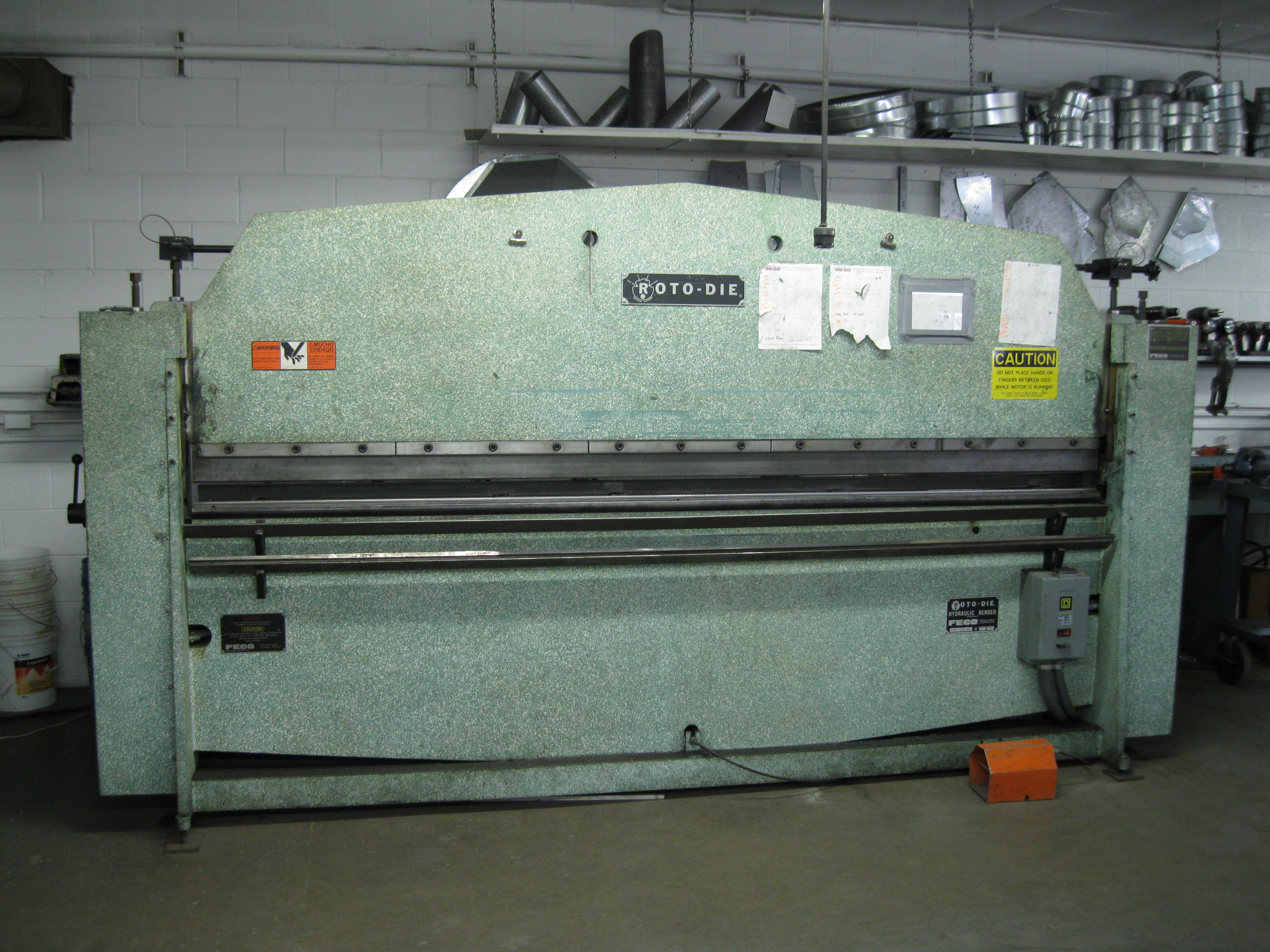


Detail Author:
- Name : Providenci Kshlerin
- Username : gene61
- Email : cormier.mabel@hackett.com
- Birthdate : 1980-01-03
- Address : 4533 Torphy Crest Sierrafort, TX 91404
- Phone : +1 (315) 459-1800
- Company : Sipes Ltd
- Job : Video Editor
- Bio : Quos sunt soluta ut et dolores esse vel. Pariatur voluptatem aliquam aut odit labore sunt voluptatibus. Quod consequatur sint quo necessitatibus.
Socials
linkedin:
- url : https://linkedin.com/in/romaine9297
- username : romaine9297
- bio : Expedita facilis quas vel est provident.
- followers : 3872
- following : 870
tiktok:
- url : https://tiktok.com/@romaine_okuneva
- username : romaine_okuneva
- bio : Doloremque similique ab amet perspiciatis facere rem quas.
- followers : 653
- following : 2140
facebook:
- url : https://facebook.com/romaine_okuneva
- username : romaine_okuneva
- bio : Voluptas nisi corporis molestiae magni.
- followers : 6862
- following : 291
instagram:
- url : https://instagram.com/romaine_okuneva
- username : romaine_okuneva
- bio : Optio nihil voluptatem sint fugit minima illum nulla et. Et suscipit omnis provident sed quod iure.
- followers : 4870
- following : 1681
twitter:
- url : https://twitter.com/rokuneva
- username : rokuneva
- bio : Sint molestias ipsa beatae. Non fuga quia odit sint optio ducimus magni. Tenetur aliquam non asperiores et.
- followers : 1907
- following : 765